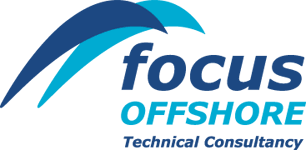 |
|
|
|
Hydrodynamic
Design
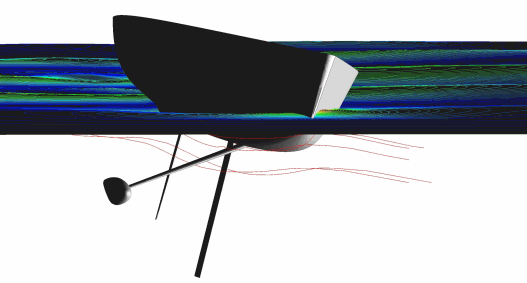
The Indian Ocean tsunami which devastated 13 countries and
killed more than 200,000 people in December 2004 was a chilling
demonstration of the power of the hydrodynamic forces which
are generated when a fluid flows over a solid object. Forces
of lower magnitude are more common in the marine environment,
but they may still be destructive or wasteful in the long
term. For example:
• An increase of just 20 microns in the surface roughness
of a ship’s hull will increase its hydrodynamic drag
– and hence the fuel required to power it – by
1 or 2%. This equates to over 2 million tonnes of fuel wasted
in a year, based on the world shipping industry’s annual
fuel consumption of 170 million tonnes.
|
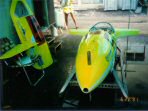 |
A fair hull reduces propulsive power
requirements |
|
• The hydrodynamic drag of an unfaired object –
and hence the towing or mooring force – may be 40% higher
than that of a similar streamlined shape.
High forces are required to tow
a blunt body |
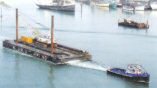 |
|
• Vortex shedding from poorly designed underwater
components causes unsteady hydrodynamic forces, leading to
premature fatigue failure. |
|
Expensive structures
may suffer premature fatigue failure due to poor hydrodynamic
design and exposure to high water flow velocities
|
|
|
|
Such problems can be avoided by careful consideration
of the surrounding flow regime and appropriate hydrodynamic
design.
Focus Offshore offers impartial consultancy and a practical
design service for:
- Hydrodynamic force analysis
- Lift and drag predictions
- Advice on drag reduction techniques
- Control surface and appendage design
- Hydrodynamic performance prediction, evaluation and optimisation
- Experimental specification for physical modelling
- Model testing, data processing and performance assessment
- Procurement of cost-effective facility hire for hydrodynamic
testing
- Technical audits and appraisals
- Provision of Computational Fluid Dynamics (CFD) flow
analysis
Representative projects:
· Hydrodynamic design of underwater vehicles [download
paper]
· Worldwide audit of hydrodynamic tests facilities
for QinetiQ Haslar
· Design of control surfaces [download
paper]
· Novel propulsion systems [download
paper]
· Non-Intrusive Methods for Detecting Laminar-Turbulent
Transition in Boundary Layer Flow |
Right:
Hydrodynamic test facilities
Bottom row, from left:
Flow visualisation of a control surface tip vortex
Colour-coded results from acoustic detection
of laminar/turbulent flow transition
Drag reduction in the design of an underwater
vehicle
Tank tests to determine manoeuvring coefficients
of an underwater vehicle
|
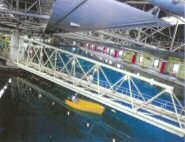
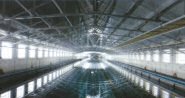
|
|
|
|
|